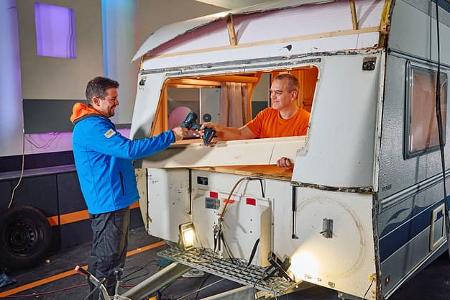
Für viele Werkstätten wäre Ferdi ein wirtschaftlicher Totalschaden. Aber genau solchen vermeintlich hoffnungslosen Fällen hat sich der Camping Doktor verschrieben. Los geht’s!
Für viele Werkstätten wäre Ferdi ein wirtschaftlicher Totalschaden. Aber genau solchen vermeintlich hoffnungslosen Fällen hat sich der Camping Doktor verschrieben. Los geht’s!
Der Schaden unseres Redaktionscaravans hat uns schwer überrascht. Dennoch haben wir es uns vorgenommen ihn zu retten.
Das Messgerät detektiert viel Feuchtigkeit unter der Verkleidung. Die Stichprobe mit dem Schraubendreher bestätigt die Messwerte eindrucksvoll.
Hier ist alles weich und klitschnass. Das Styropor (EPS) wirkt wie ein Schwamm und saugt sich voll, was das stützende Holzgerüst verrotten lässt.
Um den Schaden richtig freizulegen, müssen vorab alle Leisten weichen. Dabei ist besondere Vorsicht gefragt ...
... da die Leisten für ein so altes Schätzchen kaum noch zu bekommen sind. Ein flexibler Spachtel hilft vorsichtig Druck aufzubauen und Dichtmittel zu ...
... durchtrennen. Die beiden Bugecken des Gaskastens sind innen vielfach geschraubt und zusätzlich über Dichtmasse mit dem Bugblech verbunden.
Große Teile des Fensterrahmens sind nicht mehr zu retten und müssen abgetrennt und entfernt werden.
Alufraß und Nässe sind das Todesurteil für den unteren Teil des Fensterrahmens. Sauber ausgeschnitten, dient das Stück beim Wiederaufbau als Schablone.
Die Verbindung zwischen Seitenwand und Boden hat in den Jahren deutlich gelitten. Nach dem Entfernen aller Bleche passen sogar Finger durch den Spalt.
Wenn die einst stützenden Latten wie Mulch aus dem Aufbau rieseln, ist die Reparatur unumgänglich. Nach Meinung des Fachmannes hätte der Wagen mit dem Schaden keine Hauptuntersuchung bestehen dürfen.
Mit dem Multitool fliegen die Styropor-Fetzen. Dabei eignet sich der oszillierende Aufsatz gleichermaßen zum Lösen der Dämmung und zum Sägen der Lattung.
Wenn selbst der Finger problemlos im weichen Holzpudding einer ehemaligen Stützkonstruktion verschwindet, ist klar: Hier ist nichts zu retten. Alles muss neu gemacht werden.
Im unteren Bereich ist der Schaden größer als zunächst vermutet. Also raus mit der Sitzgruppe und den feuchten Bereich Schicht für Schicht mit dem Multitool freilegen.
Um den Ausbau der von außen geschraubten Sitzgruppen-Dachschränke zu umgehen, wird das von Klemmleisten befreite Dachblech einfach angehoben.
Auch an der Serviceklappe gibt es einen Wassereinbruch. In Folge sind der Kabelschacht, der Boden darunter und das Innenleben der Klappe beschädigt.
Nachdem der Innenboden mit dem Multitool ausgeschnitten wurde, geht es dem morschen Abschnitt der Holzlatte im Klappenrahmen an den Kragen.
Erstaunliche 15–20 Liter Wasser waren laut Kay im Aufbau gebunden.
Ein ganz anderer Schaden findet sich unten an der linken Bugecke. Risse und Brüche im Kunsstoff.
Die Reinigung der Teile vor der Reparatur ist unerlässlich. Beim Kleben und Arbeiten mit Epoxidharz sind Einweghandschuhe sinnvoll.
Gewebe-Klebeband verhindert das Durchlaufen des 2K-Klebers.
Die Glasfasern geben Stabilität und werden mit Harz steinhart.
Die Klammern werden, quer zum Riss, vorsichtig eingeschmolzen.
Bugschaden: Der Aufbau des neuen Bugbrettes beginnt mit dem zugeschnittenen Innenteil, auf dem die Holzlattung mit einem Polymerkleber vollflächig verklebt wird.
Nachdem das Fachwerk sitzt, wird es mit passend zugeschnittener Isolierung (Styropor) ausgefacht und dabei ebenfalls vollflächig verklebt.
Bevor es in den Schrott fliegt, dient das alte Bugblech als Schablone für den Neuzuschnitt mit Überlappung.
Nach dem Schneiden mit Flex und Trennscheibe werden die Schnittkanten mit einer Feile gebrochen, was auch entgraten genannt wird.
Der verwendete Kleber auf Polymerbasis kommt in Kartuschen, harmoniert mit vielen Materialien und lässt sich am Wohnwagen daher vielfältig einsetzen ...
... Nachdem der Kleber grob aufgetragen wurde, wird er mit einem sogenannten Zahnspachtel gleichmäßig verteilt.
Der Kleber muss natürlich anziehen und aushärten. Dafür wird er mit Zusatzlatten und Schraubzwingen auf Druck gebracht. Dann heißt es warten.
Nachdem das Aluminium gereinigt und der Bug abgeklebt ist, kann der neue Bugteil lackiert werden. Die Absauganlage kümmert sich um den Sprühnebel.
Nach dem Trocknen des Lackes ist das Blech gut vor Witterungseinflüssen geschützt. Die Überlappung rechts und links sowie die vollflächige Verklebung des Bleches sorgen dafür, dass der Bug nun dicht bleibt.
Da der Rahmen des Bugfensters zur Hälfte fehlt, konstruieren wir eine Art Schienung mit reichlich Überlappung. Dafür muss aber zuerst noch Styropor weichen.
Der Platz für die Stützschiene wird mit Kleber auf der originalen Innenverkleidung vorbereitet. Der Rest des ursprünglichen Rahmens endet in der Markierung.
Nachdem die Stützlatte eingepasst ist, muss der Kleber trocknen – natürlich auch hier unter Druck.
Mit dem fertigen Stützkorsett kann das fehlende Stück Fensterrahmen ausgemessen und eingepasst werden. Auch hier kommt reichlich Kleber zum Einsatz.
Gemeinsam mit einer Stützlatte direkt am seitlichen Fensterrahmen gewinnt der Bug Stück für Stück an Stabilität und ist nun vorbereitet für die Isolierung.
Als Nächstes bekommt der Bugfensterrahmen das untere Eckstück, das mit der Stichsäge an die runden Konturen der Fensterecke angepasst werden muss.
Styropor lässt sich auch mit einem Messer zuschneiden, dabei flockt es aber. Der heiße Draht des Profigeräts schneidet sauber undvor allem millimetergenau.
Als Innenverkleidung kommt eine Sperrholzschicht mit einseitig weiß versiegelter Oberfläche zum Einsatz. Sie wird vollflächig auf Lattung und Isolierung geklebt.
Mit dem originalen isolierten Eck-Element ist die Bugecke fertig. Anschließend werden noch die Schnittkanten versiegelt. Der Farbunterschied ist marginal.
Serviceklappe reparieren: Zusätzliche Holzleisten geben der früheren Schadstelle Stabilität. Zusätzlich lässt sich das eigens angefertigte Bodenstück später mit ihnen verschrauben.
Im Styroporschneider wird ein Draht erhitzt, der butterweich durchs Material schneidet und präzise, saubere Schnitte zulässt. Hier wird gerade die Dicke reduziert.
Nachdem das neue Holzfachwerk und die Styroporisolierung perfekt sitzen, wird die neue Deckplatte für den inneren Boden eingeklebt.
Die Kantenleiste direkt hinter der Außenhaut hat ein spezielles Profil. Dank hervorragend ausgestatteter Holzwerkstatt ist der Zuschnitt kein größeres Problem.
Aufgrund ihrer geringen Dicke von nur wenigen Millimetern ist bei Arbeiten an der Außenhaut Fingerspitzengefühl gefragt. Hier wird der Kleber für die neue...
... Holzlatte eingebracht. Diese wird im Anschluss mit vorsichtigen Hammerschlägen in Position gebracht. Abschließend wir das abgerundete Eckstück eingeklebt.
Vorher: Die Feuchtigkeit hat die Lattung komplett aufgeweicht und auch der Innenboden samt der darunterliegenden Isolierung ist hinüber.
Nachher: Nach der Reparatur ist alles wieder stabil. Wer Wert auf Optik legt, kann die Stelle noch mit PVC angleichen. Für den Stauraum sparen wir uns den Aufwand.
Eindichten: Der abgesackte Boden wird mit neu aufgebauten Ecken der Seitenwand verklebt und anschließend mit vier langen Edelstahlschrauben verschraubt.
Die Durchleitung für das Positionsleuchtenkabel braucht ein neues Loch, da im Unterbau eine neue Latte sitzt. Für große Durchmesser sorgt der Forstnerbohrer.
Bevor die Bug-Gürtelleiste zurück an das Fahrzeug kommt, muss sie von alter Dichtmasse befreit, gereinigt und mit neuer Dichtmasse versehen werden.
Auch das Fenster-Dichtgummi fürs große Bugfenster bekommt nach einer Reinigung ausreichend Dichtmittel ab. Was hervorquillt, kann später abgetupft werden.
Frisch gereinigt und von Rückständen befreit, wird die Kantenleiste der Seitenwand eingedichtet und verschraubt.
Zig Kartuschen Dichtmasse, Kleber und Schrauben sind im renovierten Aufbau. Die Auswahl der verwendeten Werkzeuge beschränkt sich hier im Bild auf die tragbaren Varianten.
Geschafft! Nach drei zusätzlichen Tagen ist Ferdi bereit für die Straße.