Wie entsteht ein ausgebauter Kastenwagen?
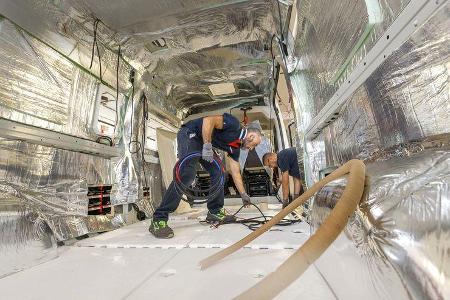
Wer wollte nicht gerne mal Mäuschen spielen und beobachten, wie so ein Campingbus ausgebaut wird. Wir haben es uns ganz genau angeschaut in der Van-Produktion von Trigano in Süditalien – und stellen Produktions-Schritte und Mitarbeiter vor.
- Eingangskontrolle
- Produktionsband
- Qualitätssicherung
- Das Werk
Auch wenn es auf den ersten Blick fast so aussieht wie beim Bau eines Spacelabs für den Weltraumeinsatz – hier entsteht ein Campingbus für den ganz irdischen Gebrauch. Bei der Wärmeisolierung der Blechkarosserie setzt Trigano Van auf ein ganz besonderes Dämmmaterial mit alukaschierter Innenseite – darum der spacige Look des frisch ausgekleideten Kastenwagens.
Trigano Van? Kenne ich nicht. Habe ich da was verpasst? Tatsächlich starteten die Campingbusse einstmals unter diesem Label, doch schon seit einigen Jahren werden die Fahrzeuge zwar weiter zentral produziert, dann aber unter den Namen von aktuell acht Marken dergroßen französische Trigano-Gruppe in jeweils eigener Ausführung verkauft. In Deutschland sind das die Marken Challenger, Chausson, Roller Team und Karmann Mobil mit der Davis-Baureihe.
Doch zurück auf Los. Die frisch produzierten Ducato-Kastenwagen werden vom Fiat-Werk nicht direkt zur Trigano-Fertigung transportiert, sondern gehen zunächst zu einem Karosseriespezialisten, der die nötigen Ausschnitte für Fenster und Bordtechnikanschlüsse ins Blech schneidert.
1. Eingangskontrolle der vorbereiteten Vans
Die Schnittkanten vor Korrosion zu schützen und mit einem Rahmen aus druckfestem EPS-Schaum zu verstärken, gehört ebenso zu seinen Aufgaben wie das Einbringen der Bodenisolierung aus gleichem Material. Dann erreichen die vorbereiteten Kastenwagen die Trigano-Fertigungshalle – alles auf denkbar kurzen Wegen, denn alle drei Werksgelände sind im selben Industriegebiet im Valdi Sangro in Süditalien beheimatet. Bevor der Ausbau beginnt, müssen die angelieferten Transporter dem prüfenden Auge von Ilaria De Iure standhalten. Die 40-jährige Eingangskontrolleurin checkt, ob das Fahrzeug der bestellten Konfiguration entspricht. Ob alle Blechausschnitte korrekt angebracht und die Kanten entgratet sind. Und ob beim Transport und den Vorarbeiten nicht etwa Schäden an Lack und Karosserie entstanden sind. Erst dann darf der Kastenwagen in die eigentliche Produktionshalle rollen.
An der ersten Station kleben geübte Hände die Dekorfolien und Schriftzüge auf die Außenhaut. Dabei ist einiges an Erfahrung und Geschick notwendig – die Einarbeitungszeit dauert üblicherweise vier Monate –, um die teils großflächigen Klebefolien präzise zu platzieren und blasenfrei aufzubringen. So wird schon frühzeitig erkennbar, welcher Marke der gerade produzierte Campingbus zuzuordnen ist. Gleich am Anfang müssen auch die Kabelstränge und Leitungen entlang der Karosserieholme verlegt werden, denn bereits im nächsten Schritt verschwinden sie schon wieder – unter den Dämmmatten der Dach- und Wandisolierung.
Dabei setzt Trigano auf eine besondere Materialkombination: 10 bis 20 Millimeter dicke Matten aus Polyestergewebe, die auf der einen Seite mit einer Klebe-, auf der anderen mit einer Alufolie kaschiert sind.Neben einer besonders guten Wärmedämmwirkung soll das Material auch eine nennenswerte Minderung der Geräuschübertragung erreichen. In der Produktion bewährt es sich außerdem durch seine einfache Verarbeitung. Die flexiblen, selbstklebenden Matten lassen sich leicht an der Blechwand und um Spriegel herum anbringen. Alle Stücke werden wiebei einem Schnittmusterbogen vorkonfektioniert und müssen dann nur noch im Fahrzeug korrekt zusammengepuzzelt werden.
Mitarbeiter
Name: Elisabetta Pagliuca Alter: 54 Funktion: Montagearbeiterin Aufgabe: Vormontage von Bordtechnikkomponenten, aktuell: Vorbereiten der Anschlüsse an der Druckpumpe. Werdegang: Stammt aus der Region, absolvierte die Sekundarschule, arbeitete vorher bei einem Automobilzulieferer, ist bereits seit 13 Jahre bei Trigano in der Vormontage beschäftigt.
2. Produktionsband: 23 Minuten pro Station und Arbeitsschritt
Das Produktionsband ist in 28 Fertigungsstationen gegliedert, die u-förmig einmal längs durch die Halle und wieder zurück angeordnet sind. Wobei man sich beim Stichwort „Band“ vielleicht ein falsches Bild macht. Da die hergestellten Produkte ja selbst Räder und Motoren aufweisen, ist kein Band im eigentlichen Sinne nötig. Alle 23 Minuten starten die Ladys und Gentlemen die Motoren und fahren eine Station weiter. Filter am Auspuff schützen die Mitarbeiter vor dem Dieselruß.
Als Nächstes kommt die Deckenverkleidung und anschließend der Fußboden ins Fahrzeug. Ein Kran mit Saughebern hilft dabei, die sperrige Bodenplatte präzise zu platzieren.
Das ist wichtig, denn Bodenplatte, Dämmschicht und Blechboden haben bereits alle nötigen Bohrungen, die nun genau übereinanderliegen müssen – etwa um den Gurtbock vorschriftsgemäß mit dem Chassis zu verschrauben. Wie bei vielen Produktionsschritten ist dabei Teamwork gefragt. Während ein Arbeiter rücklings auf einem Rollrutscher liegend unter dem Fahrzeug gegenhält, kann der andere die Schrauben von oben mit dem vorgegebenen Drehmoment anziehen.
Damit der Einbau der Möbel und der Bordtechnik schnell und reibungslos verläuft, werden in der Vormontage Gasrohre abgelängt und gebogen, Schlauchstücke an Wassertanks angebracht und ganze Schränke aus Brettern und Beschlägen zusammengefügt. Bis hin zum Küchenblock, der bereits komplett vormontiert und mit Geräten bestückt in den Ausbau gehoben, befestigt und angeschlossen wird.
„Die intelligente, schlanke Organisation der Vormontage ist einer der Schlüssel zur effektiven Produktion.“ Giancarlo Finizio, seit gut einem Jahr Trigano-Werksleiter, nutzt seine Erfahrungen aus der vorigen Tätigkeit in der Automobilindustrie, als er eine Turbolader-Produktion schlanker organisierte, nun auch hier. Erste Veränderungen brachten eine Reduktion der Zwischenlagerfläche und eine flexiblere Einsetzbarkeit der Mitarbeiter.
Zurück am Band, werden gerade Hängeschrankklappen montiert, während ein Kollege bereits die Gasversorgung der Kocherflammen kontrolliert.
Mitarbeiter
Name: Pio Polignone Alter: 50 Funktion: Lagerarbeiter Aufgabe: Belieferung der Vormontage und des Fertigungsbandes mit den benötigten Bauteilen aus dem Lager. Werdegang: Hauptschulabschluss, dann zehn Jahre in Deutschland, Ausbildung und Arbeit als Lagermeister in Spedition, vor neun Jahren zurück nach Italien, seit ein paar Jahren bei Trigano.
Name: Antonio Recchia Alter: 30 Funktion: Montagearbeiter Aufgabe: Vormontage von Möbelmodulen für den anschließenden Einbau am Fertigungsband. Werdegang: 15 Kilometer entfernt aufgewachsen, absolvierte eine Graphiker-Ausbildung, fand aber keinen passenden Job, nun seit zwei Jahren bei Trigano in der Möbelfertigung.
3. Funktionsprüfung und Qualitätskontrolle
Das emsige Treiben in und um die entstehenden Campingbusse erscheint dem Besucher ziemlich unorganisiert. Denn es wird nicht etwa Funktionsbereich für Funktionsbereich aufgebaut, sondern gleichzeitig an verschiedenen Stellen gewerkelt. Doch die Abläufe folgen einer ausgetüftelten Choreografie, die zum einen berücksichtigen muss, dass die meisten Teile nur in einer bestimmten Reihenfolge montiert werden können. Zum anderen soll der Arbeitsaufwand bei jeder Station etwa gleich groß sein, um die 23-Minuten-Taktzeit effektiv zu nutzen – aber auch das Pensum zu schaffen.
Die Funktionsprüfung der Bordtechnikkomponenten erfolgt darum bereits im Laufe der letzten Fertigungsstationen. Es wird kontrolliert, ob alle Lichter brennen, ob die Steckdosen auch Strom abgeben – inklusive der USB-Ladebuchsen. Außerdem wird die Dichtigkeit der Gasanlage mit Überdruck geprüft, gecheckt, ob Warmluft aus den Ausströmern kommt und ob alle Hähne mit Wasser versorgt werden.
40 Minuten Regenschauer muss jeder fertiggestellte Campingbus am Ende auch noch über sich ergehen lassen. So wird die Dichtigkeit der Dachhauben und Fenster überprüft. Dann folgt die finale Qualitätskontrolle, bei der mit Hilfe einer umfangreichen, Tablet-basierten Checkliste jeder Bereich des Fahrzeug. akribisch auf Vollständigkeit und Verarbeitungsqualität kontrolliert wird.
Qualitätsmanager Diego Cavuto erklärt anhand verschiedener Auswertungsgrafiken, wie das aktuelle Qualitätsniveau der Produktion überwacht wird. Beim Überschreiten vorgegebener Grenzwerte „läuten die Alarmglocken“ und es werden die Ursachen analysiert und Gegenmaßnahmen eingeleitet. Mit dem roten Aufkleber der Qualitätskontrolle auf der Frontscheibe erhält der fertige Campingbus schließlich die Freigabe. Dann wird seine Fahrgestellnummer im System der Vertriebsmitarbeiter aktiv geschaltet und die Auslieferung kann organisiert werden.
Das Trigano-Van-Werk ist aber nicht etwa nur eine reine Produktionsstätte. Es gibt auch eine Konstruktionsabteilung, die das Grundgerüst der Ausbauten und die Installation der Bordtechnik konzipiert, wie der junge Konstrukteur Enrico D’Agostino nicht ohne Stolz erklärt. Alles, was der Käufer sieht und anfassen kann, hecken dagegen die Entwickler der verschiedenen Marken aus – um den jeweiligen „Look and Feel“ zu transportieren.
Dem neugeborenen Campingbus ist es dabei vermutlich egal, welches Label er trägt, wenn er von hier auf seine erste große von hoffentlich vielen weiteren Reisen aufbricht.
Mitarbeiter
Name: Enrico D’Agostino Alter: 35 Funktion: Konstrukteur Aufgabe: Planung und Konstruktion der Bordtechnik-Installationen (Elektrik, Wasser, Gas) der Van-Modelle. Werdegang: Stammt aus der Region, studierte nach dem Gymnasium Automobiltechnik bis zum Master, arbeitete zunächst in einem Stahlbaubetrieb, nun seit zwei Jahren bei Trigano.
Name: Roberta Colangeno Alter: 38 Funktion: Qualitätskontrolleurin Aufgabe: Endkontrolle auf Vollständigkeit und Verarbeitungsqualität anhand einer detaillierten Tablet-Checkliste. Werdegang: Stammt aus L’Aquila in den Abruzzen, Wirtschaftsgymnasium, verschiedene Stellen bei Industriewäscherei, Kurierdienst und Heizungshersteller, seit zwei Jahren bei Trigano.
Name: Giancarlo Finizio Alter: 48 Funktion: Manager der Produktion Aufgabe: Leitung des Fertigungsstandorts, Produktions- und Personalplanung, verantwortlich für über 180 Mitarbeiter. Werdegang: Stammt aus der Region, studierte Elektrotechnik in Rom, arbeitete bei verschiedenen Elektronik-Unternehmen, dann bei Honeywell im Val di Sangro, seit einem Jahr bei Trigano.
Das Werk der Trigano-Van-Produktion
Kurze Wege bedeuten geringe Transportkosten. Und der Preis ist einer der wesentlichen Verkaufsfaktoren im hart umkämpften Segment der ausgebauten Ducato & Co. Darum hat die französische Trigano-Gruppe ihre Campingbusfertigung nur einen Steinwurf entfernt vom Transporterwerk SEVEL in Süditalien aufgebaut, wo Fiat, Citroën und Peugeot die Ducato-, Boxer- und Jumper-Kastenwagen herstellen.
Hohe Produktionszahlen helfen ebenso die Kosten je Fahrzeug niedrig zu halten, deshalb beziehen acht Trigano-Marken Campingbusse aus diesem Werk – in Deutschland vertrieben werden davon die Marken Challenger, Chausson, Karmann und Roller Team. In die jetzige Halle mit 10.800 m² zog die Produktion vor rund drei Jahren ein. In der vergangenen Saison 2017/18 wurden mit 181 Mitarbeitern – 165 in der Fertigung, 16 in der Verwaltung – gut 4300 Campingbusse hergestellt. Am u-förmig angeordneten Band gibt es 28 Stationen, am Tag verlassen bis zu 20 neue Fahrzeuge die Halle.