Besuch im Fiat-Werk in Italien
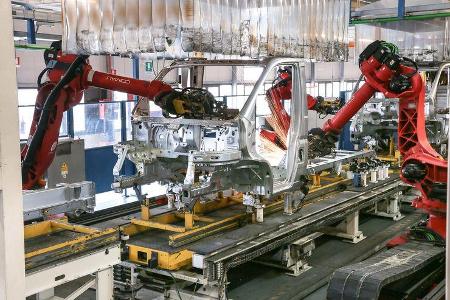
Wie genau wird das wichtigste Basisfahrzeug für Reisemobile – der Fiat Ducato – eigentlich hergestellt? Wir haben für unsere Serie „Hinter den Kulissen“ seine Geburtsstätte in Italien besucht.
Es ist ruhig rund um das Werk SEVEL, die Stimmung ist entspannt. Jetzt im Herbst bei meinem Besuch zeigt sich Süditalien von seiner schönsten Seite, bei Sonne und angenehmen 25 Grad. Aber warum ist es hier so still? Nur vereinzelt sieht man Menschen durch das parkartige Gelände zwischen den Gebäuden gehen – sonst nichts. Hier sollen jeden Tag über 1000 Exemplare des Ducato und seiner Halbgeschwister Citroën Jumper und Peugeot Boxer vom Band rollen – kaum zu glauben. Dafür müsste hier doch viel mehr Lärm und Betrieb sein – oder sind womöglich gerade Werksferien?
Zum Glück nicht, denn ich möchte mir den Herstellungsprozess des Transporters, der mit dem Slogan „Born to be a Motorhome“ antritt, ganz genau anschauen, an seiner Geburtsstätte im Val di Sangro, rund 60 Kilometer südlich von Pescara, einer Provinzstadt in der Region der Abruzzen. Dafür geht's in Karosseriewerk, Lackiererei und Endmontage.
Grundlagen im Karosseriewerk
Die Tür zum „Body Shop“, dem Karosseriewerk, öffnet sich. Okay, jetzt wird die Sache konkreter. Aus der Fata Morgana kristallisiert sich so langsam etwas Reales, das die Zahlen und Dimensionen begreifbarer werden lässt. Auf mehreren Ebenen schweben Kastenwagenhüllen und Rohfahrgestelle verschiedener Produktionsstadien kreuz und quer durch die hohe Halle. Roboterarme wirbeln Blechteile durch die Luft, andere eilen hinzu, verharren kurz, setzen unter Zischen und Funkenflug ein paar Schweißpunkte und rücken ab zur nächsten einprogrammierten Stelle.
Menschen entdecke ich erst auf den zweiten Blick, beim Kontrollieren von Werten auf Displays oder auf Gabelstaplern vorbeisausend, um Rohteile irgendwo ans Band zu liefern. Die Produktion der Blechkarosserien von Kastenwagen ist weitgehend automatisiert. Anders sieht es bei den Camper-Chassis aus. Hier lerne ich Marco Metani kennen, der mir zeigt, wie man die Schweißpunkte richtig setzt, damit aus den Blechteilen ein stabiler Flachrahmen wird.
Er ist 24, arbeitet seit zwei Jahren im Werk SEVEL und stammt aus der Region – wie rund 90 Prozent seiner Kolleginnen und Kollegen hier. Er ist froh, beim größten Arbeitgeber der Gegend einen Job mit Perspektive gefunden zu haben, und hofft, sich hier weiterentwickeln zu können. Dann eilt er zurück ans Band, um die letzten seiner Schweißpunkte zu setzen. Abhängig von der Karosserievariante sind es insgesamt 4000 bis 7000, die einen kompletten Ducato zusammenhalten. Falls Punkte fehlen, gibt es einen Rüffel von Marilena Tucci, die nach einer internen Weiterbildung nun im Bereich der Qualitätskontrolle im Karosseriewerk beschäftigt ist. Sie ist eine der über 20 Prozent weiblichen Beschäftigten im Werk und geht mit mir die Stellen durch, auf die sie besonders achtet – nicht nur die Schweißpunkte, sondern auch Kontrollbohrungen, an denen man erkennen kann, ob die Karosserieteile geometrisch korrekt zusammengefügt sind.
Zusätzlich werden in regelmäßigen Abständen Karosserien auf eine automatische Vermessungsbank gesetzt, wo eine Vielzahl von Messpunkten mit dem Laser abgetastet und mit den Konstruktionsdaten verglichen werden. Giuseppe Rotoli, Spezialist für die Wartungsplanung der Produktionsanlagen, führt mich durch die Halle und erklärt, dass es sich um das größte Karosseriewerk der ganzen Fiat-Gruppe handelt und alle Fließbänder zusammen sich auf eine Länge von rund acht Kilometern summieren. Allerdings werden in SEVEL die Karosserien nur zusammengebaut. Die verzinkten Blechteile und sonstigen Komponenten kommen von Zulieferern. Ich erzähle ihm von meiner Verblüffung über die Ruhe am Werkseingang.
Des Rätsels Lösung, verrät mir Rotoli, liegt in der geschickten Anordnung des SEVEL-Werks. Der ganze Lieferverkehr wird an der Rückseite des Geländes abgewickelt. Rund 500 Lkw und ein kompletter Zug beliefern täglich das Werk mit allen nötigen Teilen. Etwa 215 Transporter und bis zu acht Züge sorgen wiederum für den Abfluss der produzierten Kastenwagen und Fahrgestelle – täglich!
Jetzt darf ich selbst Hand anlegen. Die Montage der Fahrerhaustüren steht an. Auch wenn die Tür noch nicht mit Scheibe oder Innenverkleidung bestückt ist, hat sie schon ein ganz schönes Gewicht. Darum hilft eine Hebevorrichtung, die Pforte am laufenden Band an die Karosserie zu setzen und festzuschrauben. Beim ersten Mal ist es gar nicht so einfach, das in der Taktzeit von 55 Sekunden hinzubekommen. Immerhin, meine routinierten Fiat-Kollegen haben dafür eine kleine, amüsante Pause.
Mitarbeiter im Karosseriewerk
Name: Marco Metani Alter: 24 Funktion: Schweißer Aufgabe: Schweißpunkte setzen beim Zusammenbau der Rahmenteile. Genaue Tätigkeit wechselt wöchentlich. Werdegang: Ausbildung zum Diplom-Elektrotechniker. Stammt aus der Region, fand nicht gleich einen Arbeitsplatz. Freut sich nun, bei Fiat zu sein, wo es viele Entwicklungsmöglichkeiten gibt.
Name: Marilena Tucci Alter: 47 Funktion: Qualitätskontrolleurin Aufgabe: Kontrolle der Rohkarosserien auf fehlende Schweißpunkte oder geometrische Abweichungen. Werdegang: Seit 24 Jahren bei Fiat, arbeitete vorher als Sekretärin. Anfangs beim Schweißen und der Türmontage eingesetzt, dann 80-stündiges Training für die Qualitätssicherung.
Für Farbe sorgt die Lackiererei
Für mich heißt es jedoch, gleich weiter zur nächsten Station zu eilen, der Lackiererei. Im Obergeschoss treffe ich alte Bekannte, denn hier spuckt das Förderband die Silber schimmernden Rohkarossen wieder aus, die durch einen langen Korridor auf Stelzen vom Body zum Paint Shop wandern.
Alessandro di Nitto, frischgebackener Manager der Lackiererei, erklärt mir, dass seine Kollegen als Erstes die Motorhaube und die Türen mittels Hilfsstreben in einer halb offenen Position fixieren, damit alle Karosserieteile bei den folgenden Tauchbädern gleichmäßig benetzt werden. Zudem wird im Laderaum der Kastenwagen eine Hilfselektrode aufgehängt. Denn der folgende Prozess, Kataphorese genannt, beruht auf elektrochemischen Vorgängen. Jeder Ducato geht dabei siebenmal auf Tauchstation, wird gewaschen, entfettet, aktiviert und phosphatiert und schließlich in einem 330 Kubikmeter Grundierungsfarbe fassenden Becken bei 320-Volt-Spannung einer kathodischen Tauchlackierung unterzogen. Sie sorgt für eine besonders innige Verbindung zwischen Blech und Farbe.
Abschließend wird der Lack bei 180 Grad Celsius im Ofen getrocknet. Gut zwei Stunden dauert der ganze Prozess. Nach dem Abkühlen ziehen geschickte Hände akkurate Dichtfugen entlang der Blechstöße an den Karosserieflanken. Jede Fuge wird versiegelt, außen, wo es auf die Optik ankommt, mit einer pastenartigen Dichtkleberraupe, innen flächiger mit einem Schaum. An Letzterem darf ich mich versuchen. Die Choreografie der Bewegungen zwischen der Karosserie auf dem Band und der Spritzpistole in meiner Hand klappt beim zweiten Exemplar schon besser. Robotern überlässt man dagegen das Auftragen spezieller Akustikschäume, etwa auf dem Boden des Fahrerhauses. Sie verhindern Dröhngeräusche, die, vom Motor angeregt, sonst auftreten können.
Die Kür ist das Aufsprühen der eigentlichen Lackfarbe. Dafür stehen in jedem der beiden Paint Shops des Werks je zwei Lackierstraßen bereit. Eine ist jeweils für Metallic-Lacke ausgerüstet, die einer speziellen Behandlung mit abschließender Klarlackierung bedürfen. Über 200 reguläre Lackfarben werden angeboten. Aber auch Sondertöne können bereits ab Losgröße eins verwirklicht werden. Dreizehn Farben hat jeder Lackierroboter in petto – ansonsten muss getauscht werden. Doch auch der gelenkigste Roboterarm kommt nicht überall hin. Hier sind Paolo Cilli und seine Kollegen gefragt, die den Lackauftrag von Hand perfektionieren.
Die lackierten Blechhüllen werden ganz am Ende in gleißendes Licht gestellt. Kein Flecken und keine Runzel kann sich hier verstecken. An mindestens zehn Stellen wird die Farbbalance und die Lackdicke gemessen – 70 µm bei normalen Farben, 85 µm bei Metallic-Tönen sind gefordert. Erst dann darf die Karosserie weiter in die größte Halle wandern.
Mitarbeiter der Lackiererei
Name: Alessandro Di Nitto Alter: 36 Funktion: Manager der Lackiererei Aufgabe: Verantwortlich für den reibungslosen Ablauf und ein qualitativ hochwertiges Ergebnis der Lackiererei. Werdegang: Ingenieur der Elektrotechnik, seit zehn Jahren bei Fiat, zunächst im Alfa-Romeo-Werk/Cassino, dann bei Fiat in Serbien, seit vier Jahren im Werk SEVEL, mag die Region.
Name: Paolo Cilli Alter: 35 Funktion: Lackierer Aufgabe: Handlackieren der für die Roboter schlecht erreichbaren Stellen. Werdegang: Arbeitete nach dem Schulabschluss sechs Jahre in einer Bäckerei. Ist bereits seit 13 Jahren bei Fiat und bisher stets in der Lackiererei, entweder beim Abdichten oder beim Lackieren eingesetzt. Stammt aus der Region.
Die Hochzeit als Endmontage
Die Endmontage dominiert nicht nur flächenmäßig, mit rund 2650 Mitarbeitern ist sie auch in dieser Hinsicht das Herzstück von SEVEL. Hier wuselt es viel mehr als in den beiden vorigen Hallen, denn für die unzähligen kleinen Handgriffe, die bei der Montage nötig sind, ist der flexible Mensch immer noch am produktivsten – zumal bei einem so vielgestaltigen Fahrzeug wie dem Ducato, der in über 13.000 unterschiedlichen Konfigurationen bestellt werden kann. Und alle laufen hier bunt gemischt durch das Band.
Das erfordert einiges an Konzentration und Können von den Mitarbeitern. Der Schlüssel dazu ist die werkseigene SEVEL-Akademie, in der die Mitarbeiter gezielt qualifiziert werden – schließlich sind ausgebildete Fachkräfte in der strukturarmen Region rar gesät. Sehr willkommen sind darum auch „Rückkehrer“ wie Luciano Rosato, der mir erzählt, dass er in Deutschland aufwuchs und eine Kfz-Mechaniker-Ausbildung machte.
Später zog es ihn in die Heimat seiner Familie zurück. Im Werk hat sich der Siebenundvierzigjährige inzwischen zum Teamleiter in der Motorvormontage emporgearbeitet. Er zeigt mir, wie das Aggregat mit Katalysator und verschiedenen Schläuchen ergänzt wird, um es für den spannendsten Schritt in der Endmontage vorzubereiten: die sogenannte Hochzeit.
Dabei werden die beiden größten Baugruppen – die bereits weitgehend bestückte Karosserie und der auf einem Träger vorbereitete Motor-Fahrwerksstrang – miteinander verheiratet, zu einer hoffentlich lebenslänglichen Einheit. Räder, Scheinwerfer, Stoßstange und manches mehr, müssen noch ergänzt werden, bevor mit einem Testcomputer, der an die OBD-Schnittstelle andockt, die komplette Bordelektrik durchgecheckt wird. Durch die Endkontrolle erfolgt die finale Freigabe, aber erst wenn alle fünf Prüfgruppen „ Grünes Licht“ erhalten. Dann ist der neue Ducato geboren. Mit der Aktivierung der Fahrgestellnummer im zentralen Register wird praktisch seine Geburtsurkunde ausgestellt.
Beim abschließenden Gespräch erzählt mir Werksleiter Angelo Coppola, dass SEVEL in einem internen Qualitäts-Ranking aller Fiat-Chrysler-Werke den Silber-Status erreicht hat. Man spürt – genauso wie zuvor bei seinen Mitarbeitern –, wie stolz sie hier auf das Werk und ihren Ducato sind.
Mitarbeiter in der Endmontage
Name: Luciano Rosato Alter: 47 Funktion: Teamleiter Vormontage Aufgabe: Verantwortlich für die Arbeitsorganisation und den Ablauf am Band der Motorvormontage. Werdegang: In Deutschland aufgewachsen und ausgebildet zum Kfz-Mechaniker, seit 24 Jahren wieder in der Heimat und bei Fiat in der Montage tätig, nach Fortbildung nun Teamleiter.
Name: Angelo Coppola Alter: 57 Funktion: Werksleiter Aufgabe: Verantwortlich für den erfolgreichen Betrieb des SEVEL-Werks und für seine rund 6400 Mitarbeiter. Werdegang: Maschinenbau-Ingenieur, seit 31 Jahren bei Fiat in verschiedenen Funktionen, SEVEL-Werksleiter seit 2015, zudem Qualitätsmanager für alle italienischen Fiat-Werke, stammt aus Neapel.
Die Produktionsstätte SEVEL
Società Europea Veicoli Leggeri – kurz SEVEL genannt – ist das größte Werk für leichte Nutzfahrzeuge in Europa. In Kooperation mit der französischen PSA-Gruppe 1981 gegründet, produziert das unter Fiat-Ägide laufende Werk alle Ducato, Citroën Jumper und Peugeot Boxer für den europäischen Markt und weltweit. Im Jahr 2018 werden erstmals gut 296.000 Fahrzeuge vom Band rollen, davon rund 160.000 Ducato. Im Herbst 2018 konnte bereits das Produktionsjubiläum des sechsmillionsten Transporters gefeiert werden. Auf 1,2 Millionen Quadratmeter Gesamt- und 375.000 bebauter Fläche produzieren 6400 Mitarbeiter bis zu 1200 Fahrzeuge am Tag. Zusammen mit den rund 100 Zulieferern, die sich in der Gegend angesiedelt haben, sind es sogar etwa 12.500 Menschen, die durch das Werk in Lohn und Brot stehen.
Damit ist die Produktionsstätte auch ein wichtiger Wirtschaftsfaktor in der strukturschwachen Region der Abruzzen, die nur zu rund einem Drittel aus dem Küstenstreifen an der Adria besteht, der Rest ist Gebirge, das bis auf fast 3000 Meter hinaufragt. Rund 60 Kilometer südlich der Provinzmetropole Pescara wurde das SEVEL-Werk einst aus dem sumpfigen Boden des Sangro-Tals gestampft. Das Werk besteht im Wesentlichen aus der Karosserieproduktion, der Lackiererei und der Endmontage. Unter den mehr als 160 Produktionsstätten der Fiat-Chrysler-Groupe wurde SEVEL in einem Qualitätssicherungs-Ranking mit der Silber-Medaille ausgezeichnet. In der werkseigenen Akademie werden Mitarbeiter gezielt fortgebildet.