So werden Formel 1-Autos gebaut
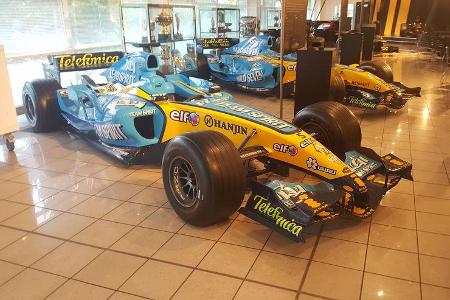
Renault will zurück an die Spitze der Formel 1. Dort, wo man mit den Weltmeistertiteln von Fernando Alonso 2005 und 2006 schon war. Eine große Chance sind die Regeländerungen im kommenden Jahr. In Enstone stehen die Uhren schon auf 2017. Wir haben den Formel 1-Rennstall in seiner englischen Heimat besucht.
Viry-Chatillon und Enstone trennen 453 Kilometer Luftlinie. In der französischen Kleinstadt, gut 20 Kilometer südlich von Paris, entwickeln etwa 500 Mitarbeiter die V6-Turbomotoren für die Formel 1-Autos von Renault und Red Bull. In Enstone, gelegen in der Grafschaft Oxfordshire im mittleren Süden Englands, hat der französische Werksrennstall seinen Hauptsitz. Zunächst schuf hier Benetton die Weltmeisterautos von Michael Schumacher, übergab dann an Renault, die wiederrum an Lotus verkauften, aber seit Dezember 2015 wieder in der Fabrik Enstone regieren. Dort arbeiten weitere 500 Mitarbeiter, die sich der Entwicklung von Chassis, Aerodynamik, Aufhängungen, Getriebe und Elektronik der gelb-schwarzen Rennwagen widmen.
Sirotkin testet im Simulator./strong>
Wir schlendern über einen Hof, vorbei an Gabelstaplern, es nieselt. Luca öffnet uns heute die Türen in der Renault.Fabrik in Enstone. Der Italiener – braun-graues Haar, Vollbart, hellblaues Hemd – führt uns in den Simulator. In einem Vorraum sitzen zwei Männer vor Computer-Bildschirmen. Mal ziehen die Monitore gerade Linien, mal Kurven mit kurzen Intervallen, mal mit langen. Daneben steht der Manager von Sergey Sirotkin, der durch eine Glaswand seinem Piloten bei der Arbeit zusieht. Der Russe ist Formel 1-Testfahrer bei Renault, und spult gerade seine Bahnen im 35 Kilometer entfernten Silverstone ab. Virtuell, versteht sich.
Sirotkin sitzt in einem Rennwagen, dem vorne die Aufhängungen und Räder fehlen. Sechs Projektoren, die wie die Äste eines Tannenbaums angeordnet in der Mitte des Raumes von der Decke hängen, werfen die Aufhängungsteile und Räder an die gekurvte Wand. Aus Sirotkins Blickwinkel kleben sie wie in der Wirklichkeit am Chassis. Für den Zuschauer wirkt es so, als ob ein Grafikfehler wie zu alten Playstation-Zeiten die Nase fälschlicherweise ausgeblendet hätte. Drei Hydraulikstelzen pro Seite bewegen Sirotkin in seinem Auto je nach Kurve hin und her. „Wir nutzen den Simulator primär als Entwicklungswerkzeug für unser Auto, und nicht dafür, dass die Fahrer trainieren können“, sagt Renault.Ingenieur Chris Dyer, der sich in der Zwischenzeit fast unbemerkt reingeschlichen hat. „Für den Grand Prix in England probieren wir heute ein paar verschiedene Lösungen aus. Wir widmen uns im Simulator aber auch schon 2017.“
Gutes Stichwort. In dieser Saison gibt es den wiederbelebten französischen Rennstall wohl nichts mehr zu holen. Die späte Entscheidung, Lotus zu übernehmen, förderte die Pace des 2016er Rennwagens nicht unbedingt. In acht Rennen holte Renault nur sechs WM-Punkte. Über Platz neun in der Konstrukteurs-WM kommen die Franzosen wohl nur noch mit viel Glück hinaus. Da macht es mehr Sinn, die laufende Saison abzuhaken, obwohl noch 13 Grand Prix zu fahren sind, und sich auf die Fahrzeugentwicklung 2017 zu stürzen. Die große Regelreform mit breiteren und bis zu fünf Sekunden schnelleren Autos könnte die goldene Chance für Renault sein, mit einem Schlag den Abstand zur Spitze zu reduzieren.
2017er Autokomponenten seit Februar im Windkanal./strong>
„Seit Februar betreiben wir ein ernsthaftes Entwicklungsprogramm für das neue Auto im Windkanal., erzählt Technik-Direktor Nick Chester. „Wir sprechen mit unseren Kollegen in Viry darüber, wie wir die Power Unit mit den neuen Regeln am sinnvollsten integrieren können.“ Der Windkanal ist nach wie vor das wichtigste Werkzeug in der Entwicklung eines Formel 1-Autos. Wir haben heute Pech. Vor der Anlage leuchtet ein rotes Licht. „Zutritt verboten“, winkt Luca ab. Fotos wären so oder so nicht erlaubt gewesen. Weil Komponenten für das nächstjährige Auto getestet werden? Wir wissen es nicht.
Immerhin nennt uns unser Tour-Guide ein paar Eckdaten. 10.000 PS stark sei der Ventilator, der die Luft auf ein 60-Prozent-Modell bläst. Ein original-großes Auto in den Windkanal zu stellen, ist laut Reglement verboten. Ein Filter nimmt der Luft die Turbulenzen. Wenn sie auf das verkleinerte Auto trifft, kann sie bis zu 50 m/s schnell sein. Das sind 180 km/h. Im Windkanal stellen die Ingenieure verschiedene Fahrzeugbewegungen nach. Zum Beispiel Roll- und Nickbewegungen. Oder sie können die Bodenfreiheit des Testmodells variieren. Selbst ein Millimeter mehr oder weniger hat große Auswirkungen auf die Fahrzeugperformance. „ Die Form des Chassis für 2017 werden wir gegen Ende Juli absegnen. Dann backen wir die ersten Chassis. Im Oktober dürften sie dann fertig sein“, verrät uns Chester noch Details aus dem Entwicklungsfahrplan für 2017.
Rapid Prototyping nennt sich der Prozess, in dem die Musterbauteile mithilfe von Lasern für den Windkanal hergestellt werden. Die Maschinen hierfür sehen aus wie abgedunkelte Brutkästen. Schicht für Schicht laminieren sie die verkleinerten Fahrzeugteile, zwischendrin markiert ein roter Laserpunkt für die Maschinen, wo sie als nächstes ansetzen müssen. So lässt sich in kurzer Zeit auch mal ein Mini-Getriebe herstellen, um beispielsweise die Kühlung zu simulieren.
CFD-Abteilung wie im Atombunker
Die CFD-Abteilung ist wie in einen Atombunker eingelassen. Auf dem Felsvorsprung wachsen Sträucher, eine Holztür führt ins Innere der Abteilung für numerische Strömungsmechanik (Computational Fluid Dynamics). Luca muss noch seine Chipkarte durchziehen und einen Code eingeben, ehe sich die Holztür öffnet. An der linken Wand hängt ein Stein mit einer Widmung: „Computational Aerodynamics Research Centre – dedicated to the memory of Dino Toso“. Zu Deutsch: Computerbasiertes Forschungszentrum für Aerodynamik – Dino Toso gewidmet. Der ehemalige Aerodynamik-Direktor von Renault starb 2008 im Alter von 39 Jahren an Krebs.
Die computergestützte Strömungssimulation ist das zweitwichtigste Werkzeug für die Aerodynamiker nach dem Windkanal. „ CFD ist gut. Aber die Daten müssen noch mit dem Windkanal und der Strecke abgeglichen werden. CFD kann vielleicht in 15 oder 20 Jahren den Windkanal unnötig machen“, erläutert Chester. In einem Nebenraum lagern die Hightech-Prozessoren in drei Reihen. Sie strahlen große Wärme ab. Entsprechend muss der Raum klimatisiert werden. „Die Prozessor-Leistung beträgt 45 Teraflops. Die Speicherkapazität liegt bei 35 Terrabytes“, sagt Luca. Man stelle sich die Stromrechnung aufs Jahr vor. „Der Windkanal verbraucht mehr“, sagt Luca. Trotzdem: Simulator, Windkanal, CFD – da verwundert es kaum, dass die großen Teams pro Jahr 250 bis 300 Millionen Euro ausgeben.
Wie entwickelt Renault zum Beispiel einen Frontflügel? Chester erklärt: „Wir beginnen mit CFD. Die Aerodynamiker testen dort eigene Ideen. Oder sie simulieren etwas, dass sie bei der Konkurrenz gesehen haben. Manchmal geht es auch nur um kleine Details, die die Strömung verbessern. Dieser Prozess kann ein paar Tage dauern, wenn es sich nur um kleine Änderungen handelt. Bei einem komplett neuen Frontflügel zieht es sich aber auch schon mal einen Monat. Dann fertigen wir die Komponenten für den Windkanal mit Rapid Prototyping und testen sie. Wenn diese Tests positiv verlaufen, geht es weiter ins Designstudio. Dort wird ein 100-Prozent-Modell erstellt. Ein komplett neuer Frontflügel braucht acht bis zehn Wochen, bis er designt und hergestellt ist.“
Carbon wird im Ofen gebacken
Es gibt viele kleine Spezialisten-Gruppen, die in einem Großraumbüro am Gesamtdesign des Formel 1-Autos arbeiten. Die Experten für die einzelnen Motorenbauteile sitzen bei Renault in Viry. Die Spezialisten für Aerodynamik, Fachingenieure für mechanische Bauteile wie Aufhängungen, Getriebedesigner und Experten für Verbundwerkstoffe arbeiten in Enstone. Den Gesamtüberblick haben Chefdesigner und technischer Direktor. In dem Fall Chester. „Ich komme um 6:30 Uhr und arbeite bis 20 Uhr abends. Zu Hause mache ich dann weiter. Ich könnte auch 48 Stunden pro Tag locker füllen.“
Während im oberen Stock der Fabrik an Computern gearbeitet wird, geht es unten ans Eingemachte. Zwei Mechaniker wühlen mit Spachteln in zwei verschiedenen Chassis. Fotografieren: verboten. Daneben stehen große gelbe Öfen, in denen die verschiedenen Autobestandteile gebacken werden. Meistens verwendet man Carbon, das wie Textilstoffe aus vielen kleinen Fasern besteht. „Ein Chassis wiegt etwa 80 Kilogramm“, sagt Luca.
In einem abgetrennten Bereich laminieren Männer und Frauen in Laborkitteln und mit Haarnetzen auf dem Kopf die verschiedenen Teile. Ins Carbon-Monocoque, das sich aus 40 verschiedenen Carbon-Typen formt, mischen sie Aluminium-Honigwaben-Verbundstoffe. Eine der Fabrikarbeiterinnen presst auf ein Carbon-Stück die Honigwaben-Struktur. Später wird das Element in einem luftdicht verschließbaren Druckbehälter (Autoklav) gebacken, und eine zweite Carbonschicht darüber gezogen. Das fertige Element sieht dann vereinfacht ausgedrückt aus wie ein Sandwich. Pro Jahr gibt Renault laut Luca rund 1,5 Millionen Pfund für Carbon aus. Aus dem Material könnte Renault.ine ein Meter breite Straße über eine Länge von 80 Kilometern pflastern.
Wir gehen um die Ecke. Dort wartet die Elektronikabteilung. Luca zeigt das Lenkrad, mit dem Kimi Räikkönen seinen Lotus zum Sieg in Abu Dhabi 2012 steuerte. „In einem Formel 1-Auto sind mehr als 250 Sensoren verbaut, die Lenkwinkel, Temperaturen, G-Kräfte, Gaspedalstellung und vieles weitere erfassen.“ Ein paar Meter weiter, vorbei am 2014er Lotus mit der charakteristischen Säbelzahnnase, stehen wir in der Werkstatt. Hier bauen die Mechaniker nach den Rennen die Autos auseinander. „Das geht in acht Stunden“, erzählt Luca. Ein Tank von ATL liegt auf dem Betonboden. „ Bitte nicht fotografieren.“ Daneben arbeiten Ingenieure in einem abgetrennten Bereich an den Getrieben. „Die Herstellung von Chassis und Getriebe beansprucht am längsten Zeit im Herstellungsprozess“, ergänzt Chester.
Nackte Zahlen entscheiden
Erst Ende April, Anfang Mai finalisierte die FIA die Regeländerungen für das kommende Jahr. Zuvor waren die technischen Rahmenbedingungen zwar abgesteckt, aber sie standen noch in der Schwebe. Trotzdem musste Renault mit dem 2017er Projekt starten, bevor die aktuelle Saison überhaupt losging. „Wenn du nicht anfängst, fällst du zurück. Du hältst dir zwei oder drei Optionen offen, und weißt, dass die Regeln in eine Richtung davon gehen könnten. Bei den Reifen wussten wir Ende letztes Jahr, wie die Dimensionen wahrscheinlich sein werden. Danach haben wir gemutmaßt, wie die 2017er Regeln ausfallen“, erzählt Chester.
Die Ingenieure und Designer begannen praktisch mit einem weißen Blatt Papier. „Wenn die Regeln konstant bleiben, übernimmst du ziemlich viele Teile. Zum Beispiel die Bremsen, die Lenkung, die Aufhängungen, ein paar Crashstrukturen. Darum formst du eine andere Verkleidung für eine bessere Performance. Aber 2017 wird das Bodywork komplett anders aussehen, und die Autos werden viel mehr Leistung haben. Die Belastungen für Bremsen, Aufhängungen und die Lenkung werden hochgehen“, sagt der Technikdirektor. „Wir können vom diesjährigen Auto noch ein paar Aerodynamik-Sachen auf das nächstjährige übertragen. Sicher nichts, was rund um den Unterboden im Heck sein wird, weil es einen größeren Diffusor und Heckflügel geben wird. Aber der Frontflügel und die Vorderreifen verbreitern sich ungefähr in gleichem Maße. Der Zusammenhang zwischen der Endplatte und dem inneren des Reifen ist ähnlich.“
Wenn es hart auf hart kommt: Wer behält dann die Oberhand? Die Motorenleute in Viry oder die Chassis.Fraktion aus Enstone? Die nackten Zahlen entscheiden. Chester nennt ein Beispiel: „Wenn wir die Kühlung ein bisschen heißer für den Motor auslegen und dadurch eine Zehntel von der Aerodynamik gewinnen, dadurch aber eineinhalb Zehntel vom Motor verlieren, dann gewinnt die Motorenabteilung.“
In unserer Fotoshow zeigen wir Ihnen einige Bilder von unserem Werksbesuch bei Renault. Anmerkung: Leider durften wir aus Geheimhaltungsgründen nur wenig fotografieren – daher ergänzen wir unsere Galerie mit Archivaufnahmen, die zum Teil bis ins Jahr 2001 zurückreichen.